Does This Spell the Decline For Aluminium Windows?
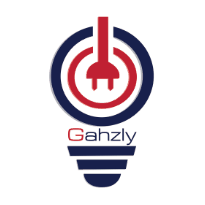
Only about once in a generation does a revolutionary new product development come along to successfully challenge all others that have gone before it – and to provide so many additional benefits over its predecessors as to render them virtually obsolete from day one.
Examples would be steel hulled ships instead of timber in the early 20th Century or the jet engine instead of propeller driven in the 1950’s. More modest examples would be music cassettes replacing gramophone records in the 1970’s, to be replaced themselves by CD’s in the 1990’s. Technology is unstoppable!
Plastic materials were first invented in 1904 but by the 1940’s these durable thermosetting resins had been blended with glass fibres for phenomenal extra strength and then moulded to be used for the hulls of fast, light weight, motor torpedo boats (MTBs) to devastating effect during WW2, recording speeds of over 40 mph. Impossible with the dead weight of steel hulls.
The same technology is still used today for RNLI Lifeboats to give maximum strength, lightness and speed. Perhaps surprisingly, the critically important nose cone on NASAs Space Shuttle comes from the same basic material.
These incredibly strong and durable composite compounds are Fibre Reinforced Polymers (FRPs) and until 1990’s could only be produced manually in a mould (hand laid) or in a high pressure flat press to make sheets for, say, high performance composite door skins.
Around the same time, Aluminium was first created and widelt used in aircraft design and for building products like windows, curtain walling, display equipment, etc. The lesser demanding window applications for housing that generally require smaller windows than offices were subsequently replaced by thermoplastic PVC but this material does not have the inherent strength to challenge aluminium in larger and more demanding applications.
Thus PVC windows grew to dominate the housing market, whilst aluminium became the dominant supplier to the non-housing commercial market.
This continued for 30 years, until now.
Two things occurred towards the end of the 20th Century to upset this status quo – namely, a) Climate Change and b) The development of ‘Pultrusion’, a continuous manufacturing process for FRP.
a) Climate Change – Gradual recognition of the causes and consequences of Climate Change has led to a succession of new legislation to reduce carbon emissions through better insulation of buildings and by developing more sustainable building practices and materials.
This has caused many specifiers to become dissatisfied with their historically traditional materials – and who are now seeking a more benign and longer lasting alternative.
Areas of discontent (supported by Greenpeace and Good Homes Alliance) are –
* Human toxicity and greenhouse gases from PVCU
* Tropical rainforest destruction and continuous maintenance of Timber
* High embodied energy and poor insulation properties of Aluminium.
Clients and specifiers, now, are increasingly demanding higher sustainability standards through increased levels of performance under BREEAM and Code for Sustainable Homes. Carbon neutral construction is also being mooted.
One of the single most important criteria in these higher standards is ‘thermal insulation’. 47% of the entire carbon emissions from UK comes from fossil fuel replacement of the heat lost from all buildings.
Windows are one of the weakest points of insulation in all buildings, accounting for over 25% of that heat loss, a significant proportion of the total UK carbon footprint.
The Achilles heel for a window’s thermal performance is not the glass – but the frame that holds it.
b) Pultrusion – Enabling GRP to be made commercially in long continuous lengths for window profiles was a significant breakthrough in Plastics development in the 1980/90’s in North America, which was introduced to UK in early 2000s. Pultrusion enabled window profiles to be made just like Aluminium or PVC but requiring no metal reinforcement for strength.
For the first time the advantages of FRP Fibreglass could be brought to bear on this specific product sector at the very time that it was coming under serious review.
The Consequences: Aluminium is unable to achieve U values below about 1.8, whilst far lower (1.2) is now being requested more and more by those striving for higher results under B.R.E.E.A.M. This is due to the very low insulation abilities of Aluminium (ironically, it is an excellent conductor), as well as to its notoriously high embodied energy from the high temperature manufacturing process. Also, it is recognised that aluminium is susceptible to a marine salt/sea spray environment which corrodes exposed aluminium. Powder coating reduces this effect until scratched or damaged but which cannot then be successfully repaired. Therefore the estimated service life is only 20 – 25 years.
Architects are now, therefore, seeking a more sustainable, longer lasting, better insulating alternative.
Whereas GRP Fibreglass as a material has consistently lower U values; is impervious to the weather and salt/sea spray; is stronger than steel; will not deform like aluminium; requires no maintenance; can be repaired and repainted if necessary; is 23% recycled; can be recycled on disposal; has pleasing slender sightlines; comes in any RAL colour and is similarly priced to aluminium whilst providing far better value and peace of mind for the client.
In summary:-
* Service life: 50 – 75 years is double that of any other low maintenance material.
* Thermal efficiency: U values of 0.9 are possible which is half that of aluminium.
* Strength: Twice the strength to weight ratio of steel, cannot deform like aluminium.
* Maintenance: Zero maintenance is required the applied colour is for aesthetics only.
* Sustainability: Achieves a potential 3½ extra credits in any B.R.E.E.A.M assessment.
The final indicator as to the new supremacy of FRP composites over aluminium is in the Aeronautical Industry, where aluminium has previously dominated for 60 years.
Breaking with this tradition for the first time, the new Boeing 787 ‘Dream-liner’ uses FRP nano-composites for 94% of the wings and fuselage. This provides reduced weight, therefore better fuel economy and lower carbon emissions, plus improved strength and durability, according to Russell Maquire, Technical Vice President, Boeing Company Inc.
Now who would argue with that?!
[ad_2]حساب مقطع الكابل الكهربائي المناسب
bedewy by askBEDEWY VISIT GAHZLY
يسعدنا زيارتكم صفحاتنا على مواقع التواصل الاجتماعي حيث نقوم بنشر عروض حصرية على موقعنا الالكتروني.
صفحتنا علي الفيسبوك هنا.
حسابنا على تويتر هنا.