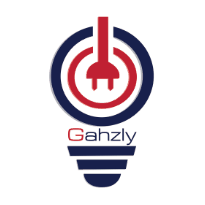
MERCEDES BENZ ALTERNATORS
Alternators & Regulators Bosch with internal regulators
DESCRIPTION
Alternators made by Bosch are conventional 3-phase, self-rectifying type alternators.
Bosch 75 through 55-amp alternators use3 negative 3 positive and diodes connected to stator windings to rectify current, Bosch 90 and 80-amp alternators use 14 diodes.
All alternators use 3 exciter diodes connected to stator windings, while the engine is running these diodes turn off the alternator indicator light and supply power to the voltage regulator, Bosch regulators are transistorized solid state and integral with alternator.
ALTERNATOR APPLICATION
Model Volts/Amps
(1) Manufacturer’s Part No.
190E 14/70 489 928
190D 14/70 489 897
All Others 14/70 N/A
(1) Bosch alternator part numbers are preceded by the numbers 0 120 or beginning with an AL lettering a number and ending with an X.
1. You can connect a voltmeter to the alternator “B+” terminal and ground, voltmeter should indicate battery voltage, if not check wiring between battery and alternator.
2. Turn ignition on and check that alternator indicator light comes on, if light does not come on, check wiring between warning light and alternator, including indicator bulb.
1. Ensure connections at battery, alternator, and starter are clean and tight, ensure alternator engine and body are properly grounded, ensure alternator belt is tight and in good condition.
2. Connect ammeter following manufacturer’s instructions, connect voltmeter leads to battery terminals.
3. Start engine and run at 3000 R.P.M. adjust carbon pile to obtain maximum alternator output, do not allow voltage to go below 12.6 volts.
4. Alternator output should equal alternator rated output, minus 16-20 amps, if reading is 16-20 amps below alternator rating, replace regulator and retest, if output is still too low, repair or replace the alternator.
REGULATOR CONTROL VOLTAGE TEST
1. Connect ammeter following manufacturer’s instructions, connect voltmeter leads to battery terminals, run engine at 3000 R.P.M.
2. Run engine until voltage stops rising, voltage should be 13.5-14.5 volts, if reading is incorrect, remove regulator and ensure brushes are longer than 6 m.m..
3. If brushes are okay and regulator fails to keep voltage within specified limits, replace regulator and retest, if voltage is still incorrect, repair or replace alternator.
OVERHAUL
DISASSEMBLY
1. Remove nut, lock washer, and pulley, remember position of spacers, Then remove fan assembly and key, scribe mark on front and rear housings, remove voltage regulator and remove screws, separate front and rear housings.
2. Disconnect capacitor from terminal; remove nut, insulators, screws and washers.
Remove stator assembly.
3. Unsolder stator from diode assembly; remove bearing wave washer or o ring from rear of housing.
3. Support front housing and carefully press out rotor, do not allow rotor to fall, remove screws securing bearing retainer, remove retainer front bearing and seal remove rear bearing from slip ring at end of rotor.
TESTING & REPAIR
Diode Assembly
1. Place ohmmeter scale on x100 scale connect ohmmeter leads across “B+” terminal and 3 stator terminals one at a time, reverse leads, ohmmeter should indicate continuity in one direction only.
2. Reconnect ohmmeter leads across negative and 3 stator terminals one at a time.
Reverse leads; ohmmeter should indicate continuity in one direction only.
3. Connect ohmmeter leads across “D+” terminal and 3 stator terminals one at a time.
Reverse leads, ohmmeter should indicate continuity in one direction only, if diodes are found to be defective, replace the diode assembly.
Fig. 3: Diode Assembly Test Diode assembly for 55 amp alternator is shown, others are similar.
1. Place ohmmeter on lowest scale, connect ohmmeter across stator leads, resistance between leads should be 14 15 ohms for 55-amp alternator and .09 10 ohms for 65 through 90 amp alternators, if resistance is incorrect, stator has open or shorted windings and must be replaced.
2. Place ohmmeter on X 1000 scale. Connect ohmmeter between stator core and stator lead, no continuity should exist, if continuity exists, stator is grounded and must be replaced.
1. Place ohmmeter on lowest scale, connect ohmmeter across slip rings, resistance should be 3 4-3.75 ohms for 55 amp alternator and 2.8 3.1 ohms for 65 through 90 amp alternators.
2. If resistance is too low, rotor has short circuit and it must be replaced if resistance is infinity no continuity, rotor has open circuit and must be replaced.
3. Place ohmmeter on x1000 scale, reconnect ohmmeter between either the slip ring and rotor core, no continuity should exist, if continuity exists, rotor is grounded and must be replaced.
4. Clean slip rings using a very fine sandpaper, rings which are worn or pitted should be turned on lathe, minimum ring diameter is 1 1/16″ 26.8 m.m. if slip rings are beyond repair, replace slip rings as outlined in steps 5 and 6.
5. Remove rear bearing from slip ring end of rotor, unsolder wires from slip rings and bend up ends of rotor winding, pull off slip rings, ensure ends of rotor winding are not damaged.
6. Insert the ends of rotor winding into slip ring and press new slip ring onto rotor, slip ring end must be 9/64″ 3.5 m.m. from end of the collar, solder rotor winding to slip ring terminals, turn rings on lathe and retest rotor, maximum slip ring run out is 0012″.03 m.m..
The Bearings
Always replace bearings, if replacement front bearing is sealed on one side only, open side must face rotor, if replacement rear bearing is sealed on one side only, open side must face away from rotor.
Brushes
Ensure brushes are longer than 6 m.m. replace if necessary, unsolder brushes from voltage regulator, solder new brushes, and do not allow solder to run into strands of brush leads.
Brush must be free to slide in holder with normal spring tension of 10-14.
REASSEMBLY
1. Install the bearing, retainer, and screws in front housing, press rotor onto housing.
Press bearing on slip ring end of the rotor, solder stator to diode assembly, exercise care when soldering near diodes due to possible heat damage.
2. Install insulators on stator assembly, assemble stator assembly and rear housing, install wave washer or O ring in rear housing, align the scribe marks and assemble front and rear housings.
3. Install key, fan assembly, and spacers, install the pulley, lock washer and nut, tighten nut to 23-29 ft. 3-4 Nm. Ensure rotor spins freely, and install voltage regulator and capacitor.
[ad_2]حساب مقطع الكابل الكهربائي المناسب
يسعدنا زيارتكم صفحاتنا على مواقع التواصل الاجتماعي حيث نقوم بنشر عروض حصرية على موقعنا الالكتروني.
صفحتنا علي الفيسبوك هنا.
حسابنا على تويتر هنا.