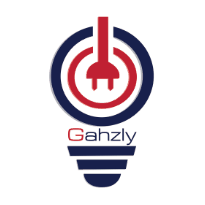
Before we re-visit our ancestors, I thought it might be interesting to see how they made battle-ready swords in Norman times.
It’s a mistake to confuse the blacksmith with the sword smith. The latter is a highly skilled tradesman, specializing just in the manufacture of swords. It took years of experience to be able to produce a weapon that was both flexible and at the same time capable of taking hard knocks to its edge without chipping.
The former, no less skilled in what he did, simply didn’t specialize in the sword smith’s skills. The blacksmith was more than capable of repairing helms, shoeing horses, repairing mail, (a most tedious business!). The blacksmith dealt in all manner of metal working, while the sword smith was a specialist.
The sword underwent a change of manufacture. Until about 900, they were pattern welded. Rods of iron and carburized iron were twisted together, repeatedly heated to white heat and beaten out. When the sword was finished and polished, a wavy line could be seen running down its length, giving it a pleasing pattern.
Improvements in steel forging after this date, however, meant that new types of swords could be produced. First, the metal was heated and hammered repeatedly, usually over six inch lengths. This was called ‘drawing out’ the sword. This was a long process, for not only did the smith have to pay close attention to making sure the cross section of the weapon didn’t become too thin, he also had to give the sword its basic shape.
At the end of this task, the metal was very brittle and had to be annealed. This is a process where the steel is softened. It’s heated to high heat, then allowed to cool very slowly. Often it was wrapped in thick layers of cloth or leather for this purpose and put aside for 24 hours.
When they were unwrapped and in their annealed state, decorations were hammered into them. First, grooves or fullers were hammered into their length. Then, names were hammered in, often the name of the sword smith himself, or his factory. The metals used for this form of decoration were latten, a type of brass. Silver, pewter or tin. They had names like “Ulfberht” or “Ingelrif”. Often, though, it would be something like “Gicelin me fecit”, “Gicelin made me”. On the reverse, a religious inscription might be hammered in. “Innominidomini”, perhaps. This was done after the sword was ground.
Often, tougher steel was welded to the edges by repeated heating and hammering, so that the sword maintained its flexibility, but remained sharp.
The next part was tempering and here the smith needed all his experience and skill. The metal is heated to a considerably lower temperature than when it’s annealed. He had to know precisely when to quench the metal. If it were done too soon, then it would be too hard. Too late, and it would become too soft again.
The medium into which they quenched the metal generally, varied from smith to smith. Some swore by honey, as they said it created fewer bubbles. Others would use salt water. Yet others would run a film of oil on top of the water, saying that the immediate quench was momentarily allayed by the oil.
The metal crossguard was slotted onto the tang, then two pieces of wood or horn, channeled out inside to take the shape of the tang were glued on, covered usually with leather and bound with thongs. The pommel was slotted over the end of the tang and hammered home.
The armourer’s workshop itself was usually a detached stone building because of the dangers of fire. The forge had a stone built hearth and an assistant or apprentice used hand operated bellows to supply the draft for the fire, which was of charcoal. There were seldom windows in these buildings. A breeze or draft from an outside source could upset the treatment of the steel. Torches gave light, as of course so did the fire.
There are a number of superb sword smiths around today, but it would be a wonderful thing indeed if a sword from the Norman era could be found in pristine condition
My thanks to Christopher Gravett and Dr. David Nicolle and their excellent book “The Normans”
[ad_2]حساب مقطع الكابل الكهربائي المناسب
يسعدنا زيارتكم صفحاتنا على مواقع التواصل الاجتماعي حيث نقوم بنشر عروض حصرية على موقعنا الالكتروني.
صفحتنا علي الفيسبوك هنا.
حسابنا على تويتر هنا.