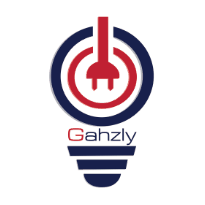
The cost, speed and quality leaps of Lean Six Sigma are obtained
through the application of appropriate tools. Following the DMAIC
improvement model of Lean Six Sigma, we will look at a number of
tools from each phase.
The Define Phase
Purpose of Define:
This phase of the Lean Six Sigma implementation identifies the
improvement opportunities and customer deliverables and defines a
scope. At the end of the define phase, we should have a project
charter, clearly identified stakeholders, a project team,
estimation of business implications, an evaluation of customer
requirements, a high level process map and project management and
communication plans.
Tools for Define:
Stakeholder Analysis:
The various stakeholders (customers, shareholders, employees) are
listed and the potential impact of the improvement project on each assessed as substantial, average, low or nil.
SIPOC diagram:
Of the tools applied in this stage of the improvement project,
perhaps the most commonly used is the SIPOC diagram. SIPOC stands
for Suppliers, Inputs, Process, Outputs and Customers. The diagram
provides a visual answer to the questions required to understand
the process: who are the primary stakeholders of this process? What
value does it create? Who is the owner of the process? What are the
inputs and who provides them? What resources are consumed by the
process? What process steps create the value?
The steps involved in creating the SIPOC diagram and the
involvement of team members in brain storming and idea generating
sessions are as important as the resulting diagram.
VOC – Voice of the Customer:
Critical to a proper definition of the improvement project is the
availability of data representing customer viewpoints and
requirements. These are collected using VOC tools like interviews,
surveys, focus groups, comment cards, suggestion/complaint boxes
etc. The definition of customer here includes internal and external
customers.
Using Kano analysis coverts raw quantitative and qualitative data
obtained from the above into clearer expressions of the value
customers place on various product and service features you offer.
Development of critical-to-quality requirements converts customer
statements, which may be imprecise, to precise requirements (valued
from the customer’s perspective) for your product or service.
The Measure Phase
Purpose of Measure:
This phase quantifies the current state of the process with respect
to cost, speed and quality and provides an idea of the gaps to be
filled. At the end of this phase, we have a detailed map of the
process, data on key input and output variables, an analysis of the
capability of the process, refined project charter and plans where
warranted by new information, and recommended actions to pick low
hanging fruits.
Tools for Measure:
Operational definition – various measures are defined so that all
team members apply the same definitions when gathering data for the
improvement project.
Process map, value stream map, complexity value stream map:
This produces a more detailed representation of the process than
the SIPOC diagram and includes such information as wait times,
processing times, resource
consumptions, process operator etc.
Cause Effect Matrix:
This tabulates causes against effects and calculates scores which
are used to rank the causes. As a measure
tool, this matrix is used to select which inputs to focus on
because of their significant impact on the process outputs.
Preliminary FMEA (failure modes and effects analysis):
This tool has a similar function to the cause and effect matrix.
All possible failures in the inputs are considered, and then
weighted according
to probability of occurrence, severity of impact on outputs and
difficulty of detection. This assessment also helps to determine
what inputs the project team should focus on.
Data collection plan:
This includes decisions as to what data (balanced between input and
output) to collect, identification of
stratification factors (these help determine patterns in the data),
determination of sample size, identification of data sources,
development of data collection sheets and assignment of data
collection duties among team members.
Pareto charts:
This is one more tool for focusing the team’s efforts on the most
important problems. A Pareto chart is a bar
chart where the horizontal axis represents categories. On the
vertical axis we can plot in descending order, the frequency of
occurrence, or cost, speed or quality impact of each category.
Where a clear Pareto effect exists, only a few of the categories
(typically 20% or less) are responsible for majority of the effects
(80% or more).
Measurement systems analysis:
The process of obtaining measurements is subjected to standard analyses to ensure reliability, repeatability and reproducibility. Other attributes of
the measurement system are stability, bias and discrimination.
Control charts:
A control chart is a run chart sequence of quantitative data with
three horizontal lines showing a centred mean and upper and lower
control limits. Control charts help to assess the nature of
variation of the process. In-control processes are expected to
yield data points randomly distributed around the mean but within
the calculated control limits.
Process capability assessment:
This tool measures of process capability assess the ability of a
process to meet functional requirements.
Several measures of capability exist. All of them are compare the
process standard deviation to the allowable range of variation as
specified by the customer.
حساب مقطع الكابل الكهربائي المناسب
يسعدنا زيارتكم صفحاتنا على مواقع التواصل الاجتماعي حيث نقوم بنشر عروض حصرية على موقعنا الالكتروني.
صفحتنا علي الفيسبوك هنا.
حسابنا على تويتر هنا.